By JOHN ANDERSON
Kinks are not just twisted things, or the name of a British Invasion rock group from the 1960s. Over a century ago in the railcar maintenance world, a kink was workshop slang for an ingenious solution to a difficult problem, a hack, if you will.
The former Milwaukee Road Southtown Yards, a giant, state-of-the-art train maintenance center that was located just east of Hiawatha Avenue and north of E Lake Street, likely implemented some of the best kinks of the time.
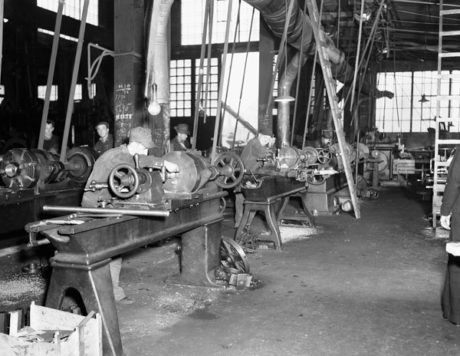
Among other facilities, Southtown Yards had a large machine shop. Steampunk fans might easily imagine how it looked at the turn of the 20th century. Machines were driven by a system of line shafts, belts, and pulleys. A line shaft was a rod that spun through power from a motor located in the powerhouse. Line shafts running from the powerhouse were buried underground enroute to the shop; inside, they were hung from the ceiling. Unfortunately, I haven’t found an actual photograph of the Southtown shop, so I will attempt to paint a picture with words.
As the hub for turning, shaping, cutting, planing, milling, and drilling the parts that kept the locomotives running, the machine shop would have been a busy place. There would have been lathes, shapers, planers, drills, bench trimmers, pipe cutters, hand millers, and horizontal boring machines. Most interesting to me would have been the ingenuity on display throughout the shop. It was the golden age of the machine, the peak of mechanical cleverness. The 1968 movie Chitty Chitty Bang Bang comes to mind. Think Caractacus Potts in his workshop but multiply the size by ten.
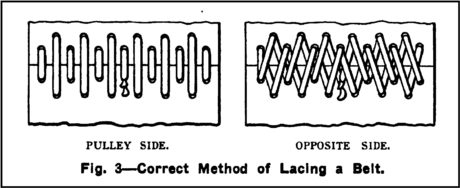
Recently, I’ve been browsing an interesting book published in 1911 called Railway Shop Kinks. (By the way, you can easily access and read it online via the Internet Archive at archive.org). Paging through the chapter on the machine shop I found some real gems.
For example, the leather belts that powered the machines came in many sizes, and were fitted on pulleys of different diameters. Some belts wore out quicker than others, so the employees on the evening maintenance shift probably inspected them all daily, making adjustments and replacements as necessary. Belts requiring maintenance were probably taken to a special shop where they might be re-laced, resized, or whatever else was necessary to make them usable again.
At that time, drive belts were laced together with strands of leather. One shop kink was to trim the belts two inches short for every ten feet so that with ends laced together they were the correct length for proper tension when fitted on the pulleys. Presumably, with wear they would have been trimmed again, punched with new holes for laces, and put back into service. Certainly, there would have been a supply of replacement belts on hand too.
Another trick was to bevel both ends of the belt and glue them together in what was called a ”cemented splice,” considered superior to lacing. All these procedures would have required precision work and a high level of craftsmanship. It would be fun today to closely study a splice in a leather belt to admire the workmanship.
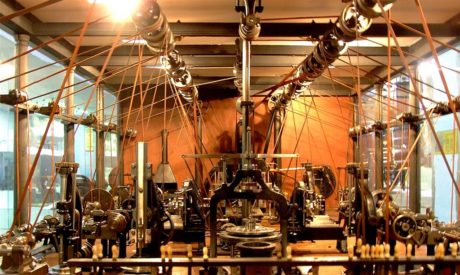
The machine shop likely had several chip boxes. These were collection points for metal cuttings. Throughout the day, cuttings from the many machines would have been added to the chip boxes, each capable of holding two tons of cuttings. After the workday, the chip boxes would have been moved by the shop crane and emptied into a nearby railway scrap car.
There would have also been a centralized tool storage area, where a skilled tool sharpener would work full-time keeping the tools like new (not exactly an ingenious idea, more in the accumulated wisdom department), and in the shop “shaft mice,” also known as shaft wipe rings, would have danced back and forth in constant motion when the line shafts rotated, keeping them clean.
There would have been many other kinks in the machine shop, and throughout the maintenance center. What I love most about discovering them was learning just how clever the craftspeople who worked in the Southtown Yards would have been. No doubt, there are many discoveries yet to be made and stories to share.
Thanks for joining me on this mechanical history treasure hunt. Next time we’ll look into the streetcar maintenance facility that once existed just southwest of Southtown Yards.
About John: John and his wife Mandy are early retiree nomads. John was a maintenance officer and administrative technician in the Air Force, a small business owner, and a light rail vehicle technician. He and Mandy are currently exploring La Paz, in Baja California for six months.